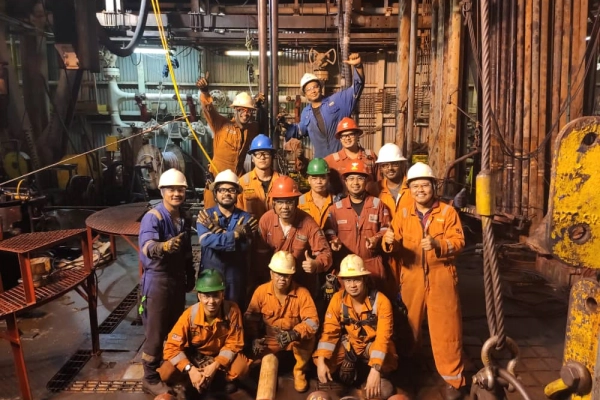
A pilot well was completed with an onshore operator in the Middle East to prove DIAL system functionality and demonstrate business value. The installation was a 'stepping stone' to more complex dual string completions. DIAL was expected to fit within the operators' wider strategic objectives of reducing drilling costs and digitalizing production.
The operator has many gas lifted requiring continuous production optimization. Flowing gradient surveys were run to determine the vertical lift performance of the well. DIAL’s sensing capabilities and remote operation had the potential to enable the operator to optimize with reduced OPEX without frequent interventions and well site visits.
A multi-drop 3.5” concentric three-unit DIAL System was installed to a depth of 7,100 ft MD inside a 7" casing. One DIAL unit for unloading at 3,400ft. MD with a second DIAL unit installed at 5,600ft. MD. The deeper DIAL unit was planned for continuous gas injection and was equipped with six valves. This allowed for fine adjustment of the gas injection rate up the maximum surface supply of 2,000 MCF/Day. A DIAL sensing unit was set at 7000ft. MD. enabling measurement of the well’s flowing bottom hole pressure (FBHP).
The real-time flowing gradient measurement presented by DIAL would enable the operator to continuously update the well model. Throughout the production phase, Silverwell provided support and guidance for the DIAL system operation and production optimization. This included extensive production modeling capability, reducing the operator’s workload for well supervision. To validate the model and DIAL data accuracy a test plan workflow was devised. This tested multiple gas injection rates to determine the optimum production rate based on the now calibrated well model. The DIAL System valves would be configured to deliver required gas injection rates through a six- valve combination of open or closed orifice ports. A well test would then be completed to compare the actual production results against the simulated estimation.
With this validation phase completed the production operators could then monitor and adjust the DIAL valve configuration from the field office without the need for frequent well site visits.
Full visibility of downhole conditions and progress of unload ensures smooth and rapid transfer to the injection point within 3 hours.
Following the unload, DIAL measured a light tubing gradient, rapidly indicating that there was no inflow from the reservoir. After acid stimulation of the perforations, the well was successfully kicked-off with DIAL.
Well tests were completed and compared against the modeled predictions. Modeling proved to be accurate. Actual liquid production matched the simulation within 1-2%. This proved the sensing accuracy and orifice port capability of the DIAL system.
Through DIAL data analysis and well testing, the optimum gas injection rate for the well was identified to be 1,000 Mcf/Day. Anything greater would have a marginal impact on fluid production. This presented an opportunity as the well had been designed for a gas lift injection rate of 2,000 Mcf/Day. The extra gas could be reallocated elsewhere within the field.
"DIAL’s digital capabilities enable continuous data analysis to determine optimum well performance"
Tubing | 3.5” 9.2 lb/ft |
Casing | 7” 29 lb/ft |
DIAL Depth | 7,100 ft. MD |
Bottom Hole Pressure | 4,800 Psi |
Bottom Hole Temp | 260 °F |
Casing Head Pressure | 1,800 Psi |
Well Head Pressure | 400 Psi |
Gas Lift Injection Rate | Gas Lift Injection Rate |