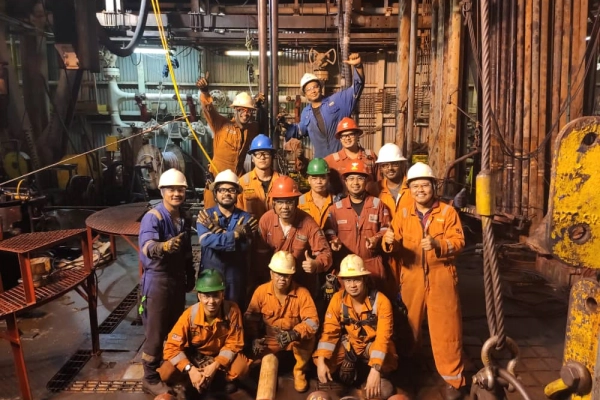
A two well pilot of the DIAL System was implemented with an onshore operator in Southeast Asia. An in-well DIAL unit enabled continuous production optimization through monitoring key production parameters and using the information to control gas injection rate without well intervention.
The candidate application was an unconventional field and the operator anticipated a rapid decline in reservoir pressure. With a conventional gas lift system, multiple flowing gradient surveys (FGS) and interventions would have been required to ensure the well was fully optimized. This equates to multiple field visits, increased OPEX expenditure, well downtime and associated HSE risk.
DIAL’s continuous pressure monitoring and surface controls offered the ideal components to safely and efficiently optimize the operator’s well performance.
Silverwell installed a DIAL unit equipped with six valves at 7,800ft MD enabling the Operator to maximize flexibility of the gas injection rate control. Pressure and temperature data from the in-well DIAL unit enabled downhole gas injection metering, which was verified against the gas injection surface flow meter throughout the pilot.
With a maximum available gas injection pressure of 1,500 psi on the surface, three gas lift stations were required to unload the well of completion fluid and reach the target gas injection depth. Reservoir and tubing pressure were sufficiently low, so gas injection could occur at the deepest possible point, just above the production packer. Conventional Injection Pressure Operated (IPO) valves and side pocket mandrels (SPM) were run above the DIAL units in station 1 and station 2 for well unloading.
The DIAL units were installed along with the Surface Control System (SCS), ¼” TEC and clamps. Silverwell also provided the services for Distributed Control System (DCS) integration. This allowed operators and production engineers to remotely monitor the well and control the DIAL System remotely, avoiding the need for wellsite visits.
To ensure the DIAL system met the installation KPIs, Periodic Flowing Gradient Surveys (FGS) were performed by the operator and verified the accuracy of the DIAL pressure and temperature sensing at depth.
Interventionless adjustment of DIAL’s multi-port injection capability ensured optimum gas injection rate.
Six well intervention savings were identified compared to a conventional gas lift system within the first 700 days of operation, resulting ~$100K OPEX savings.
Pressure and temperature sensing accuracy verified within 2.5% against the Operators flowing gradient surveys.
DIAL tubing pressure sensor identified upper IPO valve multi-point injection. Casing pressure was subsequently lowered which stabilized the well.
DIAL System run life exceeded 1,000+ days. Well eventually pulled and converted to Rod Pump
Six well intervention savings were identified compared to a conventional gas lift system
Tubing | 2-7/8” 6.4 lb/ft |
Casing | 7”29 lb/ft |
DIAL Depth | 7,800 ft. MD |
Bottom Hole Pressure | 1,500 Psi |
Bottom Hole Temp | 220 °F |
Casing Head Pressure | 1,500 Psi |
Well Head Pressure | 200 Psi |
Gas Lift Injection Rate | 500 Mcf/Day |